How-To Ensure Quality With Construction Material Testing
- Ashley Kinsela
- Apr 14
- 5 min read
Updated: Jun 18

Have you ever been in front of a new building and wondered what it takes to keep it safe, reliable, and long-lasting? Then again, strolling past the construction site, you might have seen materials like concrete, steel, and timber getting tested in all conceivable ways. Well, these tests are not just for conformity, they are part of a wider system that is called quality assurance in construction. It's a strategy that prevents you from getting nasty shocks—from structural problems to expensive fix-ups later.
Any oversight or delay in a construction project can blow up a budget and put safety at risk in today's fast-paced world. This is why construction quality management involves more than ticking boxes. It’s about guaranteeing that every material meets the standards needed to ensure buildings stand the test of time. From the foundations beneath your feet to the walls that keep out the elements, each element plays a part in overall quality.
In this blog post, you’ll learn how material testing in construction fits into a broader quality management system. We’ll explore the difference between quality control vs quality assurance in construction, highlight practical ways to develop a construction quality plan, and dive into popular testing methods for concrete, steel, and more. By the end, you’ll have a solid grasp on what it takes to create a reliable, safe structure that meets Australian standards and achieves top-notch results.
Overview Of Quality Assurance In The Construction Industry
Quality assurance within the construction sector is concerned with ensuring every stage of a project adheres to predetermined standards. It is much like a preventive mechanism whereby standards are set, proper planning is conducted, and any issues that may arise are intercepted before they become larger problems. Instead of allowing mistakes to occur, quality assurance in building construction seeks to prevent them from happening.
In most projects, a construction quality plan defines procedures such as construction material testing, regular inspections, and record-keeping. The plan is important because it keeps the whole team—engineers, contractors, suppliers, and site managers—on the same page. The plan also defines responsibilities, so everyone knows who inspects materials, who documents findings, and who makes the call if something doesn't meet the standard.
Done properly, quality control in construction projects creates a culture of consistency and responsibility. All the professionals know their part in ensuring safety and reliability. That translates to more effective communication, less surprise, and a project that goes much more smoothly from day one.
Why Material Testing Is Crucial For Construction Quality Management

Material testing in construction doesn't only validate that a sample is "good enough." Instead, it provides the information needed to ensure that materials, be they concrete, steel, timber, or aggregates, will perform compatibly with real-world conditions. This is crucial for every construction quality assurance plan since it removes guesswork and legitimizes the decision-making process.
As an example, when working with concrete, performing compressive strength tests ensures that the concrete mix has the strength to carry the loads intended for it, therefore preventing any major structural integrity issues that may occur later. Testing steel reinforcement for tensile strength guarantees that it will resist tension forces and spares one from ugly surprises such as unwanted cracking. Timber, when tested reasonably well, tells you everything about moisture content and other parameters that can lead to warping or rot.
By ensuring that everything you bring is in good condition, you are mitigating risks and ensuring excellent workmanship on the other end. Test result data from these tests feed directly into your construction quality management system, allowing you to implement process changes, train personnel accordingly, and save money through reduced rework or downtime.
The Role Of Material Testing In Construction Quality Control
Material testing is still the backbone of any construction quality management system. It is not only a requirement by law; it is a best practice for ensuring that materials meet specifications. This section examines how material testing fits into your overall plan, discusses typical methods of testing, and briefly discusses the necessity of building quality control.
How Material Testing is Incorporated into A Construction Quality Management System
Essentially, material testing in construction is the practical verification of whether or not your design assumptions are valid. If your design of concrete demands a specific compressive strength, tests on materials confirm you've met it. The same applies to aggregates, steel reinforcement, or timber. All these findings are input into project reports to enable informed decisions regarding adjustment or rectification in case of shortfalls in tests.
Common Testing Methods For Construction Materials
Construction quality control usually includes tests such as the slump test (to determine the workability of fresh concrete), tensile testing (to determine steel's stretch without failure), and moisture content testing (for wood). These tests may be done onsite with mobile equipment or in a specialized lab using sophisticated machinery. Either method, the most important thing is accuracy, consistency, and proper documentation.
Building Quality Control Measures
When establishing building quality control procedures, it is beneficial to incorporate a combination of onsite visual examinations, sample laboratory testing, and even digital monitoring equipment. By stacking various approaches, your staff has several directions to detect potential defects. This combined strategy lowers the chances of overlooking concealed defects that may affect safety, schedules, and costs.
Implementing A Quality Management System In Construction Projects
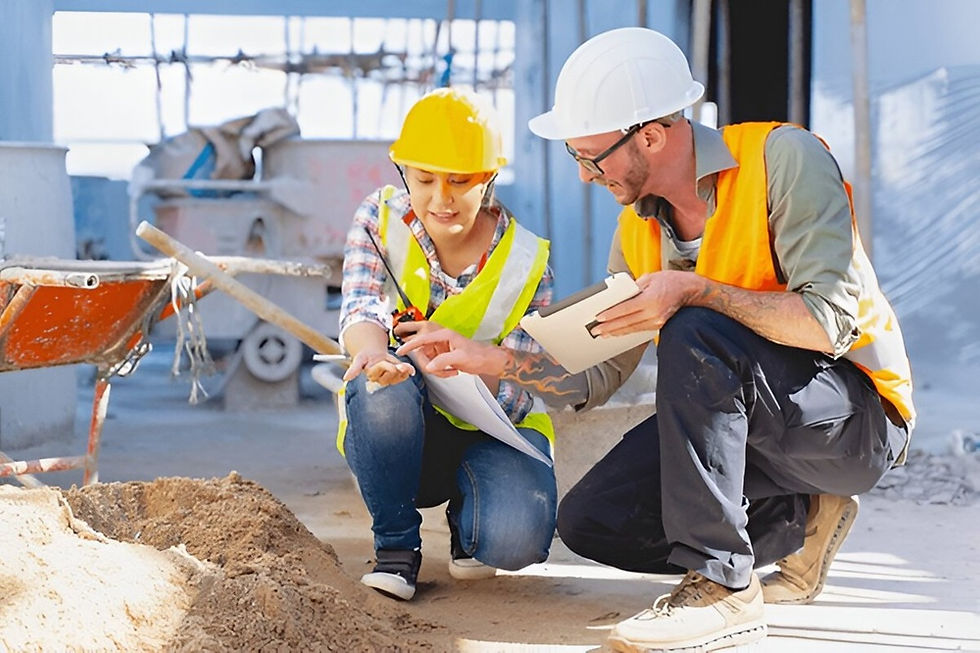
Once you’ve decided on the core principles of quality assurance in construction projects, the next step is organising them into a functioning quality management system in construction. This system provides a structured approach for everything from initial planning to final handover.
Planning And Documentation Strategies
Begin with creating thorough checklists and calendars. Record every test, inspection, and meeting. This log serves to monitor progress, maintain accountability, and provide room for improvement in subsequent projects. Computer programs can make this easier, providing real-time feedback regarding delays or issues.
Setting Up A Quality Management Policy: Key Considerations
Your document of policy construction of quality management should reflect your organisation's values. For example, if sustainability is a priority, choose materials which are environmental standards compliant and write that in your policy. Ensure the policy is available and readable for all stakeholders, ranging from the site workers to the project managers.
Routine Audits And Continuous Improvement
Regular audits enable you to gauge whether your plan is being executed correctly. They also provide you with the opportunity to identify small problems before they become big ones. Feedback loops come into play here: if audits repeatedly indicate a specific problem, modify your processes accordingly. With time, this process of monitoring, learning, and adapting creates continuous improvement in your projects.
Conclusion
By now, you would have noticed how important construction material testing is to the success of any construction project in Australia. From learning the distinction between quality control and quality assurance in construction to appreciating the importance of a quality assurance plan for construction projects, there's much to consider. By including testing of concrete, steel, timber, and other essential materials, you minimize risks, save time, and enhance trust among stakeholders.
The point is, quality management on construction projects isn't merely a matter of being compliant with minimal standards. It's about constructing buildings that are safe, durable, and as good as can be. Effective quality management on construction sites ensures that every action—mixing the concrete, installing the wires, final checks—is done to precision and care.
So, whatever you're building – a huge commercial building or a tiny house – putting quality assurance at the center of your plan can make all the difference. By ensuring materials meet the right tests and that everyone in the team is aware of them, you lay the foundations for a successful construction project. Done properly, it's good for everyone, from the site laborers who can take pride in their work to the future inhabitants who'll live or work within those strong, safe walls.
Comments